scrubguru.com
is for sale!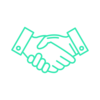
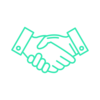
The simple, safe way to buy domain names
No matter what kind of domain you want to buy or lease, we make the transfer simple and safe.
Here’s how it worksMeet the owner of scrubguru.com
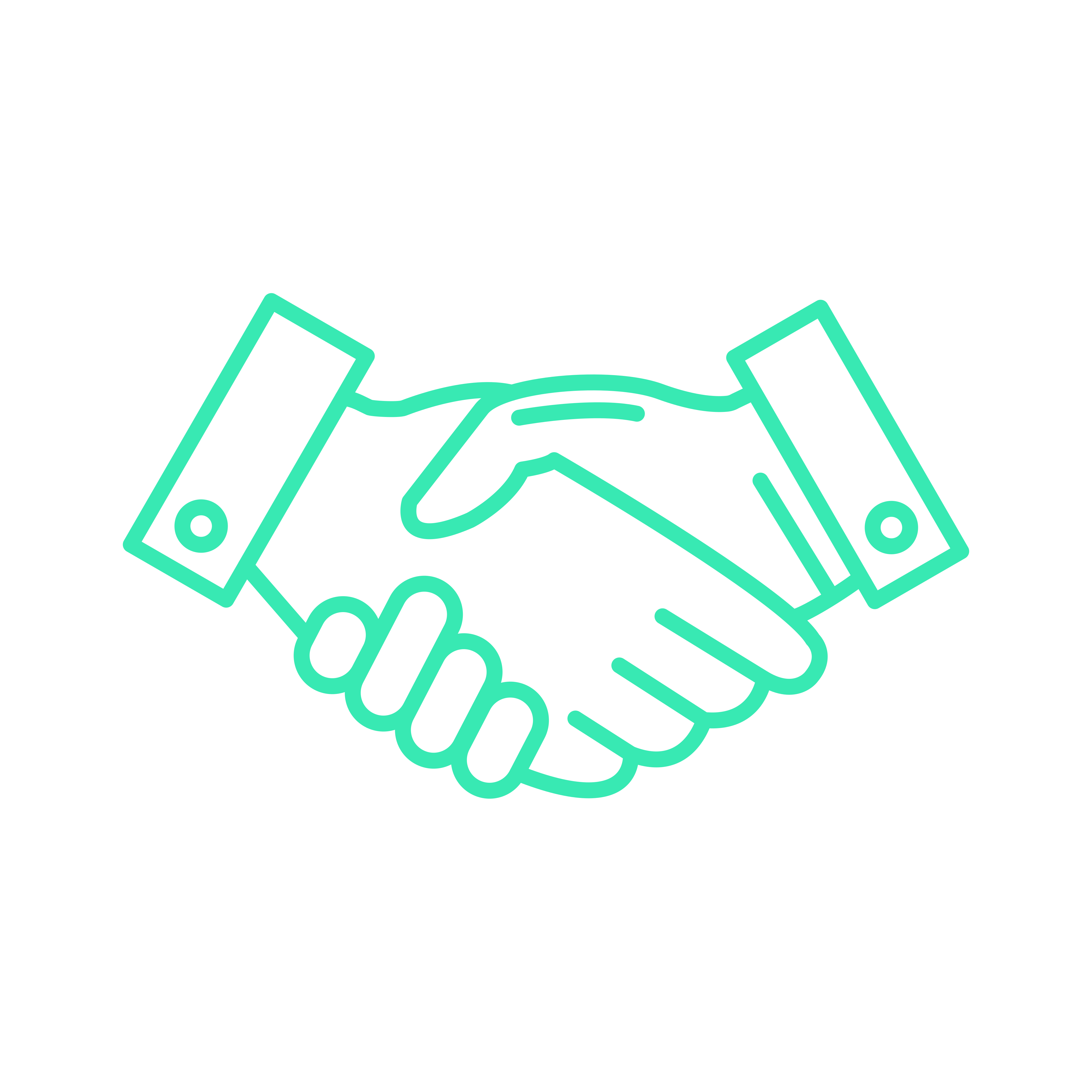
Domain seller
Member since 2019-05-07